Supply chain challenges
A leading supermarket faced inefficiencies in their inventory and fulfillment processes, which resulted in high order inaccuracies, slow order processing times, and increased customer returns. They needed to enhance visibility, improve KPI monitoring, and optimize employee performance to overcome these issues.
Algo’s solution
Algo partnered with the supermarket to enhance visibility and process optimization, providing actionable insights into their fulfillment and inventory systems. By centralizing data and closely monitoring KPIs, the supermarket improved overall fulfillment efficiency and employee performance.
The results
Through Algo’s solutions, the supermarket achieved significant improvements in fulfillment accuracy, reduced lead times, and lowered customer returns. These operational gains helped the supermarket regain control over its supply chain and set a foundation for future growth.
- 20% Increase in Order Picking Accuracy: Over six weeks, the supermarket achieved a 20% improvement in picking accuracy, reducing errors and enhancing customer satisfaction.
- 12% Decrease in Order Lead Time: Optimized fulfillment processes led to a significant reduction in order processing times, improving overall throughput.
- 25% Reduction in Customer Return Rate: By addressing inaccuracies in dispatching, the supermarket saw a 25% decrease in customer returns, cutting down on costs and improving service quality.
- Improved Warehouse Efficiency: Enhanced employee performance and optimized labor allocation increased warehouse productivity, setting the stage for long-term operational improvements.
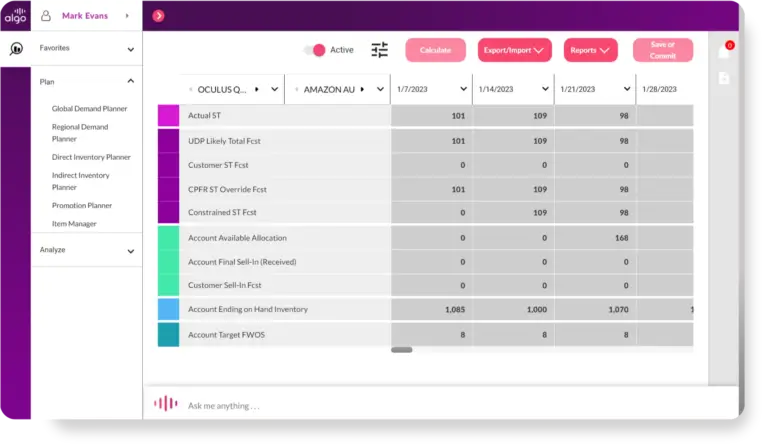